Der Motor des Minsker Motorrads zeichnet sich durch seine Verfügbarkeit zur Selbstverstärkung aus. Gleichzeitig steigert es nicht nur die Leistung auf 15 PS, sondern wird auch sparsamer und mit der Gründlichkeit der Arbeit auch langlebiger.
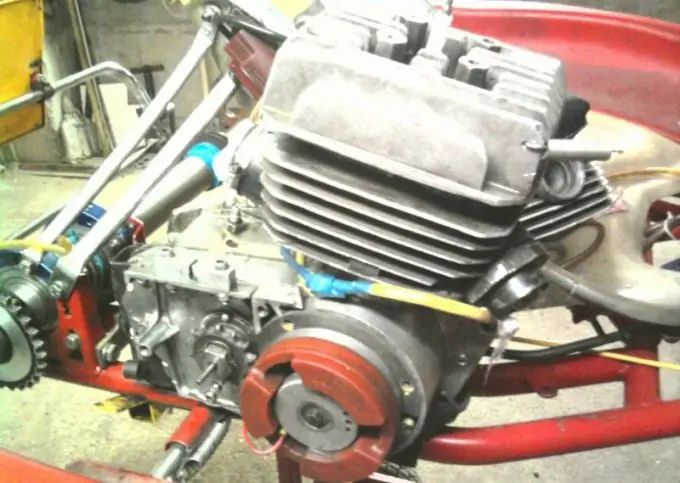
Anleitung
Schritt 1
Entscheiden Sie sich für den Zustand des Motors. Die ideale Option wäre eine neue und eingelaufene. Wenn der Originalmotor alt ist, besorgen Sie sich eine neue Kurbelwelle, Kolben mit Ringen, Lagern, Manschetten und stimmen Sie sich auf die mühevolle Arbeit ein. Zerlegen Sie zunächst das Aggregat vollständig in seine Einzelteile.
Schritt 2
Die Ausrichtung der Fenster im Liner mit den Kanälen im Zylindermantel durch Abisolieren erreichen. Stellen Sie gleichzeitig sicher, dass die Wandstärke des Mantels und des Kurbelgehäusehalses mindestens 3 mm beträgt. Verwenden Sie zum Bearbeiten von Kanälen einen Bohrer mit einem Satz Fräser und Schaber. Erzielen Sie Symmetrie und Sauberkeit der Oberfläche der Spülkanäle. Wenn die Oberfläche der Kanäle nach der Bearbeitung glatt aussieht und sich anfühlt, ist es nicht erforderlich, sie zu polieren. Achten Sie darauf, die Höhe der oberen Bypassöffnungen und den vertikalen Abblasewinkel unverändert zu lassen. Machen Sie die Vorderkante des Bypass-Fensters scharf und sägen Sie die Ober- und Unterkante des oberen Spülfensters entlang eines Radius gleich der Dicke der Hülse ab.
Schritt 3
Prüfen Sie, ob der Zylindermantel frei in das ohne Dichtung montierte Kurbelgehäuse passt. Entfernen Sie bei Bedarf überschüssiges Metall aus dem Kurbelgehäusehals. Passen Sie die Bypasskanäle zwischen Mantel und Kurbelgehäuse in einem Muster an, das der Kontur der Mantelbypasskanäle folgt. Die Auskleidungsschürze darf die Bypasskanäle nicht blockieren. Bei Überlappung den Sturz entfernen und die Verkleidungsfenster an die Kurbelgehäusefenster anpassen. Den Einlasskanal nachbohren, sodass ein glatter und stufenloser Übergang von einem runden Diffusor zu einem rechteckigen Diffusor mit Rundungen zum Auslasskanal entsteht.
Schritt 4
Richten Sie den Auslasskanal gut aus und achten Sie darauf, ihn zu polieren. Feilen Sie die obere und untere Kante des Fensters in eine ovale Form. Fasen Sie den Auslass und die oberen Bypass-Ports ab. Auch die Kolbenringe anfasen und die Ringe mit Mattchrom abdecken. Feilen Sie die Lücke im Ringschloss auf 0,2-0,3 mm. Die Oberfläche der Zylinderlaufbuchse durch Schleifen, Honen oder Läppen bearbeiten. Bringen Sie den Spalt zwischen Kolbenhemd und Zylinderbohrung auf 0,04-0,05 mm.
Schritt 5
Behandeln Sie die Kolbenschaftfenster so, dass sie zu den Zylindermantelfenstern passen. Kanten am Kolbenhemd mit einem Radius von 0,5 mm abrunden. Das Kolbenhemd selbst polieren. Am unteren Totpunkt darf der Kolben die Unterkante des oberen Bypassanschlusses nicht abdecken. Dazu entweder die Abflachungen entfernen oder den Kolbenboden im Radius von 70 mm auf das erforderliche Maß schleifen. Lassen Sie die Unterseite des Kolbens nicht dünner als 5 mm. Fräsen Sie die Enden der Pleuelaugen so, dass sich deren Abmessungen um nicht mehr als 0,1 mm unterscheiden. Erleichtern Sie den Kolbenbolzen mit einer Nut unter dem Konus, um seine Arbeitsfläche vor Beschädigungen zu schützen.
Schritt 6
Prüfen Sie das Radialspiel im oberen und unteren Pleuellager. Sie sollten nicht mehr als 8 Mikrometer (oben) und 12 Mikrometer (unten) betragen. Wenn das Spiel größer als diese Werte ist, die Kurbelwelle durch eine neue ersetzen. Die Kurbelwellenfinger separat aus jeder Wange herausdrücken. Verschließen Sie die serienmäßigen Wuchtlöcher mit Aluminium und gleichen Sie dessen Gewicht mit Bleistopfen aus, die in die unteren Teile der Kurbelwellenwangen gesteckt werden. Schleifen Sie die Wangen selbst auf einen Durchmesser von 100 mm, um eine Beschädigung der Stifte zu vermeiden. Den Durchmesser der Stifte selbst mit feinem Schleifpapier auf 17 mm reduzieren.
Schritt 7
Erzielen Sie eine reibungslose Verbindung aller Oberflächen der Pleuelstange, um Risiken an den Kontakten zu vermeiden. Achten Sie darauf, die Außenfläche der Pleuelstange zu polieren. Vor dem Zusammenbau der Kurbelwelle alle Teile des unteren Pleuellagers mit Molybdändisulfid einreiben. Drücken Sie den Kurbelzapfen ohne Verzerrungen. In diesem Fall sollte das Axialspiel zwischen dem unteren Kopf der Pleuelstange und der Wange 1, 6-1, 7 mm betragen. Kurbelwelle sorgfältig zentrieren und auswuchten.
Schritt 8
Die Oberfläche des Kurbelgehäuses sauber aufbohren. Befestigen Sie die Aluminiumringe mit Epoxidkleber und 3 M5 Senkkopfschrauben. Füllen Sie alle Lücken im Kurbelgehäuse mit Epoxidharz gefüllt mit Aluminiumpulver oder Weichmacher. Nach der Verarbeitung Kurbelgehäuse mit Dichtmittel ohne Dichtung montieren. Beim Einbau die Kurbelwelle mit zwei Unterlegscheiben gegen Längsverschiebung sichern. Montieren Sie alle Motorverschraubungen mit einem anaeroben Dichtmittel.